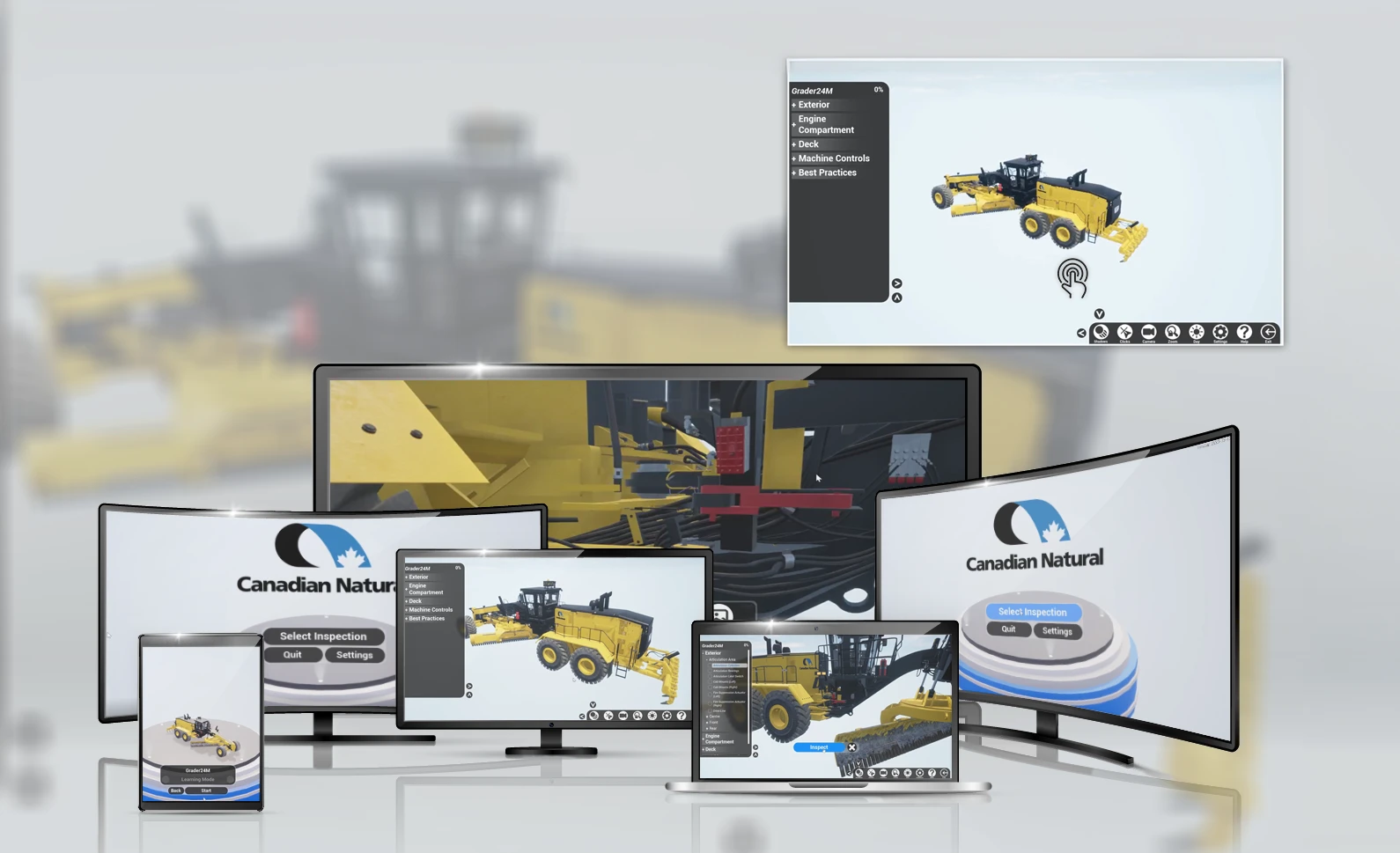
The training team at CNRL Horizon, who have worked with various learning teams at TLN for several years, engaged the XR team about creating a learning tool that utilizes 3D models of some of the large pieces of equipment (such as shovels, dozers, and graders) that they train new employees on. This training is intended to prepare personnel to work on or around this equipment during their shifts.
The intention behind the creation of this learning application was to minimize the impact of requiring a piece of equipment to be taken out of production for training while maintaining, and even increasing, the quality of the learning and training being provided. This would provide a tool that had the capabilities to better prepare employees to be job-ready, or “fit for the field”. This also gave the application its name, “Fit4Field”, which is an acronym that stands for:
Formalized
Interactive
Trainer
4
Field
Inspections
Evaluations
Lessons and
Development of Operators
Part of the plan to create the Fit4Field application was versatility; CNRL wanted to use Fit4Field as an application their training team could use during instructor-led classroom sessions on a large touchscreen television, but they also saw the value in creating a tool that learners could go back to and reference for continued learning after the initial training took place. This could be accessed either through their large screen display or through another touchscreen device, such as a tablet, smartphone, or touchscreen computer display. This would reduce the number of training hours required to get employees prepared for working safely and effectively with these pieces of heavy equipment and improve their competency and confidence on the job. And it would allow their equipment to stay in production longer with fewer disruptions for training, increasing their profitability by hundreds of thousands of dollars over time.
Each piece of modelled equipment is divided into sections, such as “Engine” or “Front End”, and important parts or points of interest are identified for individual focus. When one of these points is selected from the application’s menu, the entire model is centred around this position. Users can then move the model 360-degrees, pivoting around this point to give context as to where it is located. Information is also included on these focus points and can include text, static visuals, documents, or videos that allow for learners to gain knowledge about each component and see a realistic visual of what it looks like on the real equipment they will see in the field.
The CNRL Horizon training team has been utilizing Fit4Field as part of their employee training regimen on-site for many months, and the results have been very positive. It allows their instructors to provide sessions that blend the best aspects of classroom training with the “real-life” feel of doing an in-person inspection or walkthrough. It also allows their trainers to be able to provide engaging training sessions, including one-on-one teachable moments that may happen in scheduled training or otherwise. The fact that their users can go back to the tool again and again for reference is also a big boost to their continued learning efforts. One possibility that they are excited about is using Fit4Field to eliminate the need for a field inspection as part of their training process. While Fit4Field is already greatly reducing the need for this in-person training, they see Fit4Field as being effective enough as to soon replace this step entirely.
The positive financial impact that Fit4Field is having is that it has reduced the time that a piece of equipment needs to be pulled out of production for training; production schedules do not have to be slowed, altered, or stopped to accommodate these longer training sessions. Because they can stay in production, the operations at Horizon can continue more consistently and, in turn, more profitably. While the primary goal of the Fit4Field project was to have an effective, flexible training tool, this ROI is a big reason why they are excited to continue with it in the future.
Fit4Field has proven to give their operators a level of understanding that computer-based training modules were not achieving, and they have noticed an enormous increase in the retention of information when training with Fit4Field. It allows them to train to a standard at an early stage that wasn’t achievable before. It also sets the CNRL Horizon training team apart from their industry peers in terms of equipment training. They feel Fit4Field has allowed them to separate themselves and elevate their training efforts higher than they have ever been, surpassing other training teams that prepare equipment operators for field work.
Leave a comment
You must be logged in to post a comment.